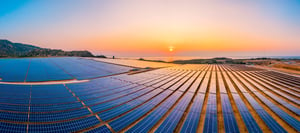
Monitor the Efficiency of Inverters to Avoid Unexpected Losses
This case study presents the successful implementation of an automated solution to collect AC power and DC power data at inverter level across a portfolio of 60 PV assets, consisting of a total of 6,000 string inverters. The solution calculates the efficiency of each inverter as a percentage and sends the management team a daily list of those below the predefined efficiency threshold. This solution has improved operational efficiency, enabled accurate monitoring of inverter efficiency and reduced the risk of production losses in the portfolio.
CONTEXT
The client, a leading solar company with its own assets, managed a portfolio of 60 PV assets with an average of 100 string inverters in each plant. Evaluating and monitoring the efficiency of the inverters was critical to ensure maximum production and profitability of the portfolio.
CHALLENGES
The client faced the following challenges:
- Manual Monitoring: Manually collecting AC power and DC power data from each inverter via the SCADA of each of the plants was difficult and time consuming.
- Manual Efficiency Calculations: Manually calculating the efficiency of each inverter and generating reports in MS Excel consumed time and resources, diverting from spotting performance issues.
- Problem Detection: Detecting low-efficiency inverters through the defined process required constant effort and could result in unidentified production losses.
SOLUTION
Quintas Analytics developed and implemented a complete automated solution to address the challenges mentioned above:
- Automated Data Collection: A system was designed to automatically collect AC and DC power data at inverter level from the SCADA of each plant.
- Automated Efficiency Calculations: The solution calculated the efficiency of each inverter using the collected data.
- Automatic Notifications of Low Efficiency: In the event of an inverter falling below the efficiency threshold determined by the asset manager, the solution sent a notification to the management team.
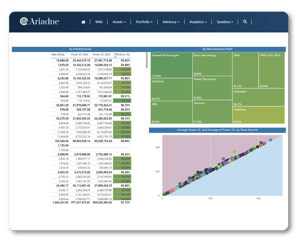
RESULTS AND BENEFITS
Implementing the solution had a positive impact on operational efficiency and production optimisation:
1. Efficient Automation: The solution eliminated the need for manual data collection and calculations in MS Excel.
2. Early Detection: Automatic notification enabled the early detection of inverters with low efficiency.
3. Reduced Risks: The solution minimised the risk of unidentified production losses.
4. Optimised Production: Accurate monitoring allowed measures to be taken to maximise production as soon as the efficiency of the inverters was reduced.
5. Efficient Operations: The management team was able to focus on implementing proactive solutions based on automatic efficiency calculations, rather than the performance of manual tasks.
CONCLUSIONS
The implemented solution for automated inverter efficiency monitoring in a PV portfolio proved highly valuable in improving operational efficiency and optimising production. Process automation, data collection and automatic efficiency calculations provided essential tools for effective and profitable management. This solution sets a valuable example for the management of similar projects in the field of solar energy and maintenance of critical components.